You’ll find that properly securing your crash cymbals can make the difference between crisp, controlled sound and unwanted rattling during performances. While the process might seem straightforward, many drummers struggle with achieving the right balance of tension in their cymbal straps. Whether you’re working with traditional leather or modern nylon straps, mastering the correct tying technique will enhance your cymbal’s resonance and protect your investment from potential damage.
Key Takeaways
Thread the strap through the bottom hole, cross underneath, and pull through opposite top holes for even tension.
Pull straps snug while allowing natural cymbal movement, avoiding overtightening that could choke the sound.
Secure leather straps with a square knot after achieving desired tension, ensuring equal pressure on both sides.
Position mounting components correctly: bottom felt, cymbal seat, top felt, and washer on the threaded rod.
Test cymbal swing after tying to ensure fluid motion and clear, bright overtones without excessive tilt.
Understanding Different Types of Cymbal Straps
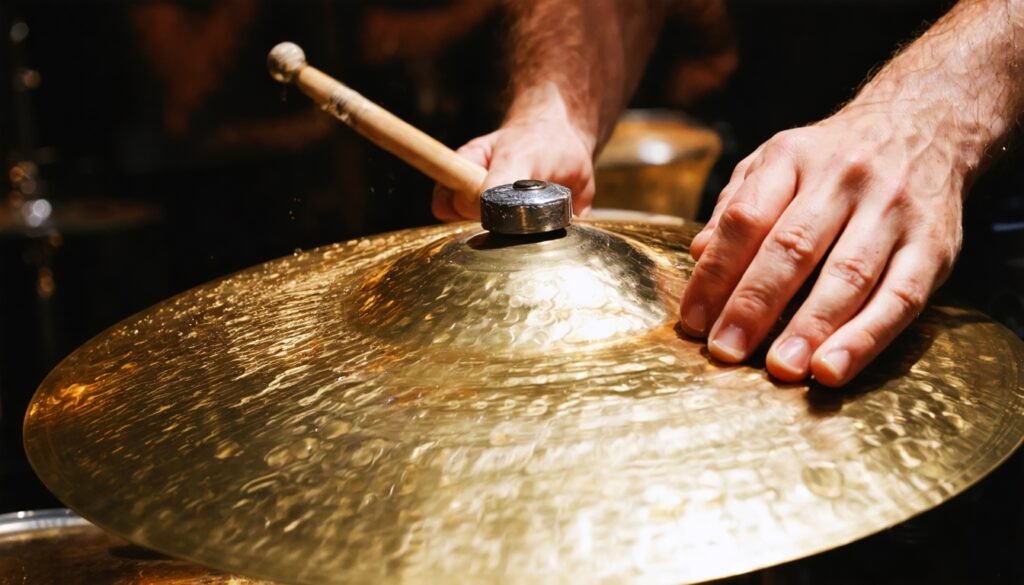
Cymbal straps come in several distinct varieties, each with specific advantages for different playing situations. The most common strap types include leather, nylon, and synthetic composites. Leather straps offer traditional feel and durability but require more maintenance, while nylon straps provide weather resistance and consistent tension.
Material differences considerably affect your cymbal’s response and feel. Premium leather straps deliver warm, natural sustain and excellent control, though they’ll stretch over time.
Synthetic straps maintain their tension better and won’t deteriorate in humid conditions. You’ll find that many professional drummers prefer leather for recording but opt for nylon’s reliability during touring.
Some modern hybrid straps combine multiple materials to balance durability with feel, offering the best of both traditional and contemporary designs.
Essential Tools and Materials Needed
For properly securing your crash cymbal, you’ll need several essential tools and materials before beginning the installation process. Most cymbal brands recommend using leather or nylon strap materials, each offering distinct advantages.
You’ll require a pair of sharp scissors or a utility knife for precise cutting, along with a measuring tape to guarantee proper strap length.
Essential items include the cymbal strap itself, a felt washer for both top and bottom positions, and a proper-sized wing nut that matches your cymbal stand’s threading.
If you’re using leather straps, you’ll also need a leather hole punch to create clean, properly-sized holes. Keep a marker handy for measuring points, and consider having spare strap materials available in case adjustments are needed.
Proper Cymbal Mount Preparation
Before installing your crash cymbal straps, you’ll need to thoroughly clean all mounting components with a dry microfiber cloth to remove dust, oxidation, and debris that could affect performance.
Inspect the cymbal seat, felts, wing nuts, and threading for signs of wear, stripping, or damage that might compromise stability.
Position your mounting components in the correct sequence: bottom felt, cymbal seat, top felt, and washer, ensuring they’re perfectly centered on the cymbal stand’s threaded rod.
Clean All Mount Parts
Start by thoroughly cleaning all components of your cymbal mounting assembly, including the felt pads, sleeves, washers, and wing nuts.
Using proper cymbal cleaning techniques, remove any dust, debris, or oxidation that’s accumulated on the metal parts with a soft microfiber cloth and specialized cymbal cleaner.
Pay special attention to the threading on both the mounting post and wing nuts, as buildup here can affect proper tightening.
Following equipment maintenance tips, inspect each felt pad for wear or compression and clean them with a gentle brush to restore their protective properties.
Don’t forget to examine the plastic sleeve for cracks or damage. If you notice any deterioration in these components, it’s best to replace them before proceeding with the strap installation.
Check Hardware For Damage
While inspecting your cymbal mounting hardware, you’ll need to carefully examine each component for signs of structural compromise or wear. Pay special attention to the wing nuts, washers, and mounting posts where metal fatigue commonly occurs.
Look for hairline cracks, stripped threading, or deformation that could affect the cymbal’s stability.
Perform detailed visual inspections of the felts and rubber components, checking for compression damage or deterioration. These parts are essential for proper cymbal function and sound quality.
Don’t overlook the mounting bracket’s connection points and any hinged mechanisms. If you discover any damaged components, immediate hardware replacement is imperative to prevent cymbal damage and maintain peak performance.
Even minor imperfections in the mounting system can lead to unwanted vibrations or potential equipment failure during performances.
Align Mounting Components Correctly
Once you’ve confirmed your hardware is in good condition, proper alignment of the cymbal mounting components becomes essential for ideal performance and protection.
Start by positioning the bottom felt washer flat against the cymbal stand‘s threaded post. Make sure it’s centered and level to provide an even foundation for your crash cymbal.
Place the cymbal on the bottom felt, making sure the bell’s center hole aligns perfectly with the threaded post. The top felt washer should rest evenly on the cymbal’s bell, maintaining proper cymbal alignment throughout the assembly.
Your mounting precision at this stage directly affects the cymbal’s movement and sound quality. Check that all components are parallel to each other and that there’s no tilting or off-center positioning before proceeding to secure the strap.
Basic Leather Strap Tying Technique
Threading leather straps through a crash cymbal’s mounting holes requires proper technique to guarantee stability and best sound. The basic tying techniques you’ll use depend on your strap material options, but leather remains the most common choice for its durability and tonal characteristics.
- Insert the leather strap through the bottom mounting hole, leaving equal lengths on both sides.
- Cross the straps underneath the cymbal, forming an X pattern.
- Thread each strap end through the opposite top mounting hole.
- Pull both ends firmly to remove any slack, ensuring even tension.
- Secure the straps with a square knot on top, trimming excess material if needed.
These steps create a secure mounting that prevents unwanted movement while allowing the cymbal to resonate freely during performance.
Advanced Nylon Strap Methods
When working with nylon cymbal straps, you’ll find two advanced tying methods particularly effective: the Double Loop and Rear Cross Pattern.
The Double Loop method creates enhanced tension control by threading the strap twice through the cymbal’s center hole before securing it with a locking knot.
The Rear Cross Pattern offers superior stability by crisscrossing the straps behind the cymbal’s bell, which minimizes unwanted cymbal movement during aggressive playing.
Double Loop Method
As drummers advance in their cymbal mounting techniques, the double loop method offers enhanced stability and control over traditional single-loop configurations. The key to success lies in proper strap length adjustment and precise loop formation.
- Begin by threading the strap through both cymbal holes, ensuring equal length on both sides.
- Create your first loop by folding the strap back through itself, maintaining tight tension.
- Form the second loop by repeating the process on the opposite end, creating symmetrical loops.
- Adjust both loops simultaneously until you achieve balanced tension and ideal cymbal height.
- Test the stability by gently moving the cymbal – it should remain firm but allow natural movement.
When executed correctly, the double loop method provides superior cymbal control while reducing unwanted movement during performance, particularly beneficial for heavier crash cymbals and intense playing styles.
Rear Cross Pattern
The rear cross pattern elevates cymbal mounting to a professional level by incorporating an intricate crossing technique behind the cymbal’s bell.
You’ll weave the nylon straps through the cymbal’s mounting holes, creating a distinctive X-pattern on the underside of the bell. This advanced method distributes tension more evenly across the cymbal’s surface.
To execute this pattern, thread both straps through opposite holes, then cross them behind the bell before securing them to the stand.
Your rear strap techniques should focus on maintaining equal tension while avoiding overtightening. The crossing pattern considerably enhances cymbal durability by reducing stress points and preventing metal-on-metal contact.
When properly executed, this mounting style allows for ideal swing and natural resonance while providing superior protection for your investment.
Adjusting Strap Tension for Optimal Sound
Proper tension in your crash cymbal straps plays a critical role in achieving peak resonance and sustain. The way you adjust your leather straps directly impacts both sound projection and tonal balance.
You’ll need to find the sweet spot between too tight, which chokes the cymbal, and too loose, which causes unwanted wobble.
- Pull the straps snug enough that the cymbal sits firmly but can still move freely
- Test the swing by gently moving the cymbal – it should have a fluid motion
- Listen for clear, bright overtones when striking the cymbal at different velocities
- Check that the cymbal doesn’t tilt excessively during play
- Readjust tension if you hear any buzzing or wavering in the sustained notes
Make minor adjustments until you achieve maximum resonance while maintaining control during performance.
Common Tying Mistakes to Avoid
When tying crash cymbal straps, you’ll need to avoid overtightening, which can cause premature leather breakage and compromise the cymbal’s natural resonance.
Don’t mix leather and synthetic strap types on the same cymbal mount, as their different tensile properties will create inconsistent responses and potentially damage your cymbal.
Maintain equal tension across all mounting points by carefully matching the pull force on each strap, ensuring balanced suspension and ideal cymbal movement.
Overtightening Leads to Breaks
Many drummers inadvertently damage their crash cymbals by overtightening the straps, creating excessive tension that can lead to stress fractures and cracks.
You’ll need to understand the overtightening risks and maintain proper tension to protect your investment.
- Allow enough slack for natural cymbal movement during playing
- Check for visible stress marks around the center hole
- Listen for high-pitched squealing when the cymbal moves
- Verify you can rotate the cymbal with moderate resistance
- Maintain a finger-width gap between the felt washers
When you’re tightening the straps, stop as soon as the cymbal feels secure but still moves freely.
If you start noticing hairline cracks or stress fractures near the bell, you’ve likely overtightened the strap.
Remember that proper tension extends your cymbal’s lifespan and preserves its tonal characteristics.
Mixed Strap Types Together
Mixing different types of cymbal straps together can seriously compromise your crash cymbal’s stability and sound quality.
When you combine leather with nylon straps or synthetic materials with natural ones, you’re creating inconsistent tension points that affect your cymbal’s performance.
Different strap materials have unique stretching properties and durability characteristics. For example, leather straps will stretch and react to humidity differently than nylon ones.
This mixing of materials can lead to uneven wear, causing one side of your cymbal to sit higher than the other. You’ll notice this manifests as wobbling during play and unwanted overtones in your sound.
Always use matching pairs of straps from the same manufacturer and material type to guarantee consistent tension, reliable performance, and maximum strap durability.
Uneven Tension Between Straps
Uneven tension between cymbal straps ranks among the most common setup errors drummers make, even after selecting matching materials.
The inconsistent pressure distribution can lead to unstable cymbal movement and potential damage to both the cymbal and mounting hardware.
- Always check that each strap carries equal weight when securing the cymbal
- Consider the strap material effects, as leather stretches differently than synthetic materials
- Perform tension adjustments systematically, moving from one strap to the next in sequence
- Test the cymbal’s movement after each uneven tension adjustment to ascertain balanced swing
- Listen for any unusual sounds during play that might indicate misaligned pressure points
When you’re setting up, pull each strap with similar force and verify the cymbal sits level.
This prevents unnecessary wear on both the straps and the cymbal’s center hole.
Maintenance and Care for Cymbal Straps
Proper maintenance of your cymbal straps can greatly extend their lifespan and guarantee consistent performance during play. To maximize strap longevity, inspect them regularly for signs of wear, fraying, or stress points where they contact the cymbal’s bell.
Store your cymbals in a controlled environment, as excessive humidity can weaken leather straps and promote mold growth. For leather straps, apply a specialized leather conditioner every few months to prevent cracking and maintain flexibility.
If you’re using synthetic straps, wipe them down with a damp cloth to remove accumulated dust and sweat. Replace straps immediately if you notice significant wear or damage. Don’t wait until they fail during a performance.
As part of your cymbal care routine, rotate strap positions periodically to distribute wear evenly across all contact points.
Troubleshooting Loose Cymbal Issues
While loose cymbals can considerably impact your performance quality, most issues stem from incorrect strap tension or improper mounting techniques.
To guarantee peak cymbal stability and maximize strap longevity, you’ll need to address common problems systematically.
- Check that your straps haven’t stretched beyond their elastic limit – replace them if they’ve lost their original tension.
- Verify the tightness of all wing nuts and confirm they’re properly threaded.
- Inspect the cymbal clutch for wear and confirm it’s gripping the strap effectively.
- Make sure your cymbal tilter isn’t causing uneven pressure on the strap.
- Double-check that you haven’t overtightened the felts, which can cause the strap to slip.
If these adjustments don’t resolve your loose cymbal issues, consider replacing your mounting hardware or switching to a different strap material.
Alternative Securing Methods and Tips
Beyond traditional leather and nylon straps, drummers have several innovative options for securing their crash cymbals. You can utilize quick-release wing nuts, which allow for rapid cymbal changes while maintaining stability.
Another effective method involves using rubber gaskets paired with felt washers, providing both protection and secure mounting.
When exploring different securing techniques, consider using dual-lock fasteners or specialized cymbal clips that offer tool-free adjustment. For safety considerations, always verify your chosen method prevents metal-on-metal contact and allows proper cymbal movement.
You’ll want to inspect mounting hardware regularly and replace worn components immediately. Modern synthetic materials like reinforced polymers can offer superior durability compared to traditional straps, though they may affect tonal characteristics slightly.
Whatever method you choose, proper tension is vital for peak sound and cymbal longevity.
Conclusion
By mastering proper cymbal strap tying techniques, you’ll guarantee ideal resonance and prevent your crash cymbals from becoming as unstable as a telegraph wire in a storm. Whether you’re using traditional leather or modern nylon straps, remember to maintain consistent tension, employ appropriate knot techniques, and regularly inspect your mounting hardware. With these skills, you’ll achieve professional-grade cymbal performance and protect your investment for years to come.