You might be surprised to learn that ancient cymbal makers used meteorite iron in their earliest designs. Today’s cymbals rely primarily on precise bronze alloy formulations, with the ratio of copper to tin determining both sound character and durability. While B20 bronze dominates professional-grade cymbals, manufacturers also work with B8, B12, and B15 alloys, each offering distinct tonal properties. Understanding these metal compositions is essential for selecting the right cymbal for your sound.
Key Takeaways
Drum cymbals are primarily made from bronze alloys, with B8 (92% copper, 8% tin) and B20 (80% copper, 20% tin) being most common.
B8 bronze creates bright, focused tones for rock music, while B20 bronze produces rich overtones ideal for jazz and orchestra.
Some entry-level cymbals use MS63 brass, consisting of 63% copper and 37% zinc, offering punchy and focused sounds.
Manufacturers may add trace elements like silver or phosphorus to the bronze alloys to enhance specific sound qualities.
The metal composition directly influences the cymbal’s fundamental tone, sustain, projection, and overall sonic character.
The History of Cymbal Materials
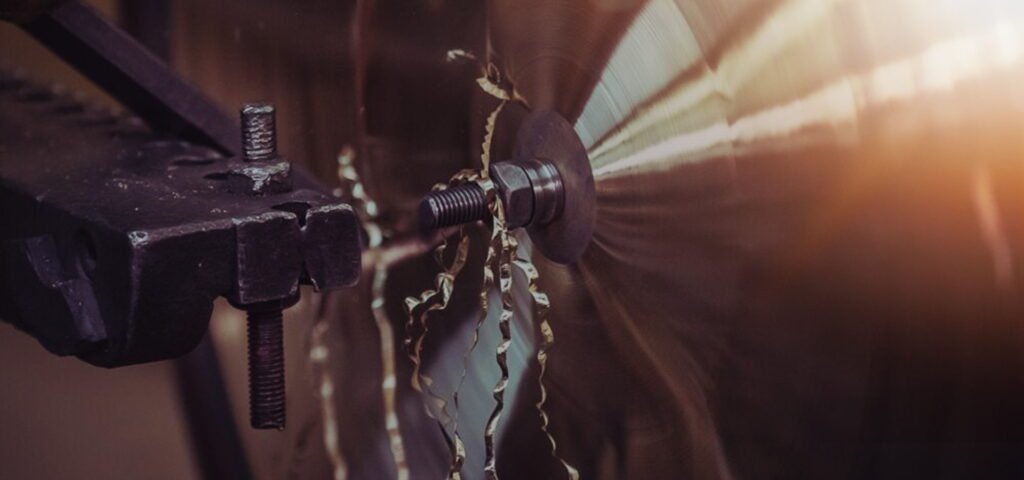
The evolution of cymbal materials traces back to ancient Bronze Age metalworking, when craftsmen first discovered that copper alloyed with tin produced bronze with superior acoustic properties. You’ll find that early cymbals contained roughly 80% copper and 20% tin, though exact ratios varied across cultures and regions.
Throughout cymbal evolution, metalworkers experimented with different bronze compositions. Chinese craftsmen incorporated higher tin contents, while Turkish artisans developed B8 bronze (92% copper, 8% tin), which became a standard for centuries. By the 1600s, you’d see B20 bronze (80% copper, 20% tin) emerge as the premium alloy, offering enhanced resonance and durability.
The cultural significance of cymbal metallurgy extended beyond sound, as different societies prized various finishes and patinas. Today’s manufacturing processes still rely on these time-tested bronze formulations, though modern techniques have refined grain structures and tempering methods for improved tonal qualities.
Common Metal Alloys in Modern Cymbals
Building upon centuries of metallurgical advancement, modern cymbal manufacturing centers on four primary bronze alloys: B8, B20, B12, and B15. These popular cymbal alloys each contain specific ratios of copper to tin, directly affecting their sound characteristics and performance qualities. You’ll find that B8 (92% copper, 8% tin) produces bright, focused tones, while B20 (80% copper, 20% tin) delivers complex, warm sounds.
When exploring alloy sound characteristics, you’ll notice these key differences:
- B8 bronze offers excellent projection and cutting power, making it ideal for rock and metal genres
- B20 bronze provides rich overtones and superior sustain, preferred in jazz and orchestral settings
- B12 and B15 alloys deliver balanced intermediate tones, bridging the gap between B8’s brightness and B20’s warmth
Manufacturers often add trace elements like silver or phosphorus to their proprietary blends, further refining the cymbal’s tonal qualities and durability.
Manufacturing Process and Metal Treatment
Modern cymbal manufacturing begins with casting molten bronze into circular blanks, where precise temperature control and cooling rates critically affect the metal’s crystalline structure. You’ll find that metal melting temperatures typically range between 1,900-2,000°F to achieve ideal fluidity and grain formation during the casting process.
After casting, manufacturers shape these blanks through a combination of hot and cold rolling, which compresses and strengthens the metal while reducing its thickness. The material then undergoes multiple heating and quenching cycles to achieve specific hardness levels. You’ll see that custom cymbals often receive specialized heat treatments to produce distinct tonal characteristics.
The final steps include hammering (either by machine or hand), lathing to create grooves, and edge profiling. Each process alters the metal’s internal structure and stress patterns, directly influencing the cymbal’s sound. Manufacturers often apply proprietary finishing treatments to protect the metal and enhance its acoustic properties.
Different Metals for Different Sound Types
Metal selection stands at the core of cymbal sound characteristics, extending beyond the manufacturing techniques into the domain of alloy formulation. You’ll find that bronze properties dominate premium cymbal manufacturing, with B20 (80% copper, 20% tin) being the most coveted composition for its rich, complex overtones. Brass versatility offers a more affordable alternative, delivering brighter, more direct sounds that cut through in high-volume situations.
When selecting cymbals based on metal composition, consider these essential factors:
- B8 bronze (92% copper, 8% tin) produces crisp, bright tones ideal for rock and pop
- B20 bronze delivers warm, sophisticated sounds preferred in jazz and orchestral settings
- MS63 brass (63% copper, 37% zinc) creates punchy, focused notes perfect for beginners
You’ll notice that each metal composition affects not only the cymbal’s fundamental tone but also its sustain, projection, and frequency response. The interplay between metal purity and alloying elements directly influences your cymbal’s voice.
Cymbal Care and Metal Maintenance
To preserve your cymbal’s acoustic properties and structural integrity, proper maintenance of its metallic surface becomes essential. You’ll need to perform regular cymbal cleaning using non-abrasive, specialized solutions that won’t compromise the metal’s molecular structure or patina. Apply these cleaners with microfiber cloths, moving in circular motions that follow the cymbal’s lathing patterns.
Corrosion prevention requires controlling environmental factors that affect your cymbals’ metallurgical stability. Store your cymbals in cases with moisture-absorbing silica packets when not in use, and maintain room temperature conditions between 65-75°F. After performances, wipe down your cymbals with a dry cloth to remove fingerprints and perspiration, as these contain acids that can deteriorate the metal alloys. If you’re dealing with B8 or B20 bronze cymbals, avoid using harsh chemical cleaners that might disrupt the copper-tin ratios at the surface level. Instead, opt for pH-neutral solutions specifically formulated for musical instruments.
Conclusion
You’ll find that cymbal composition mirrors the evolution of metallurgy itself – just as ancient smiths discovered bronze’s singing qualities, today’s B20 alloys produce those warm overtones you’re seeking. The precise balance of copper and tin, like the carefully measured ratios in a chemist’s lab, determines your cymbal’s voice. Whether you’re playing B8’s bright attack or B20’s complex resonance, you’re wielding centuries of metalworking expertise.