Recent industry data shows that CNC-driven cymbal manufacturing has reduced production variance by 87% compared to traditional hand-crafted methods. You’ll find today’s precision cymbal making relies on five cutting-edge computer numerical control techniques that merge artisanal expertise with digital accuracy. Understanding these innovations reveals how modern manufacturers achieve consistent, professional-grade sound while maintaining the nuanced characteristics that musicians demand.
Key Takeaways
Multi-zone CNC lathing systems create precise grooves across cymbal surfaces simultaneously, ensuring consistent tonal patterns and frequency responses.
Digital-controlled hammering employs sensor-guided impact systems to achieve precise node placement and reproducible sound characteristics.
Computer mapping technology scans cymbal surfaces with laser precision, creating detailed 3D models for optimized manufacturing processes.
Automated thermal monitoring systems maintain precise temperature control during heat treatment, ensuring optimal metal crystalline structure.
CNC edge profiling uses variable feed rates and real-time tool wear compensation to achieve precise edge geometries.
Automated Multi-Zone Lathing Systems
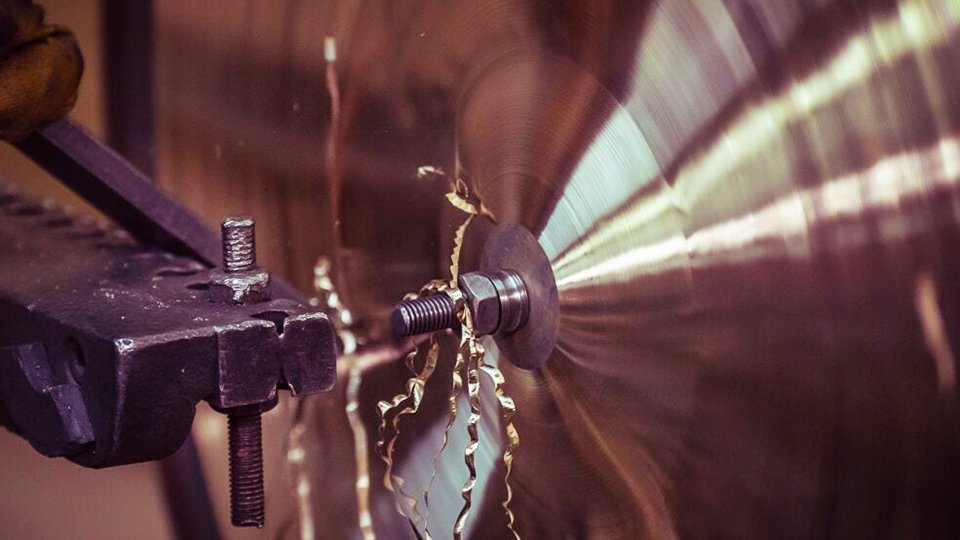
Automated multi-zone lathing systems represent a significant advancement in cymbal manufacturing precision. You’ll find these systems utilize advanced CNC integration to create precise grooves and tonal patterns across multiple cymbal zones simultaneously. The technology allows you to program specific cutting depths, speeds, and patterns for each distinct area of the cymbal’s surface.
Through automated efficiencies, you’re able to achieve consistent results across production runs while maintaining the intricate specifications required for professional-grade cymbals. The system divides the cymbal’s surface into programmable zones, each receiving unique lathing treatments that influence frequency response and sustain characteristics. You can modify parameters such as cutting angle, tool pressure, and rotation speed for each zone independently.
The precision control extends to micro-adjustments in groove spacing and depth, ensuring that your final product meets exact tonal requirements while maintaining structural integrity throughout the manufacturing process.
Precision-Controlled Digital Hammering
While traditional cymbal hammering relies on manual techniques, precision-controlled digital hammering has revolutionized the manufacturing process through computer-guided impact systems. You’ll find that these systems utilize advanced sensors to map the cymbal’s surface, creating a detailed topographical analysis before any strikes occur.
The digital impact patterns you’re implementing can be adjusted with microscopic precision, allowing for consistent node placement and harmonic development. You’ll notice how the system monitors each strike through real-time acoustic analysis, adapting the force and frequency of impacts based on the cymbal’s resonant response. By controlling variables like strike depth, spacing, and pattern density, you’re able to achieve specific tonal characteristics that were previously difficult to replicate.
When you’re programming these systems, you can store and recall successful hammering patterns, ensuring batch-to-batch consistency while maintaining the ability to fine-tune individual cymbals based on their unique metallurgical properties.
Computer-Mapped Surface Profiling
Modern surface profiling employs high-resolution laser scanning to create detailed 3D models of cymbal surfaces. You’ll find that these computer-mapped profiles capture every nuance of the metal’s topography, measuring variations down to microns. The scanning process generates millions of data points that create an exact digital replica of the cymbal’s surface characteristics.
Through advanced computer modeling software, you can analyze these scans to identify ideal tonal zones and structural patterns. The surface analysis reveals microscopic hammer marks, groove depths, and lathing patterns that influence the cymbal’s acoustic properties. You’re able to compare these profiles against reference models of vintage or high-performing cymbals, ensuring consistency in manufacturing.
This data-driven approach lets you make precise adjustments to CNC hammering patterns and lathing specifications, maintaining strict quality control throughout production. The digital profiles serve as blueprints for reproducing specific cymbal characteristics across multiple manufacturing runs.
Heat Treatment and Thermal Monitoring
Through precise thermal control systems, you’ll achieve ideal crystalline structures in the cymbal’s metal alloy during heat treatment. Modern CNC-integrated furnaces monitor temperatures at multiple points, ensuring uniform heating across the cymbal’s surface. You’ll need to maintain tight control over heating rates, typically between 15-20°C per minute, to prevent thermal stress or warping.
Your heat treatment processes must follow specific temperature curves, with digital sensors tracking the metal’s transformation phases. The thermal monitoring systems will alert you to any deviations from preset parameters, allowing real-time adjustments. You’ll observe the material’s response through integrated pyrometers, which measure surface temperatures without contact. During quenching, automated cooling systems regulate the rate of temperature decrease, preserving the desired metallurgical properties. The CNC system logs all thermal data, enabling you to replicate successful heat treatment cycles and maintain consistent cymbal quality across production runs.
Edge Profile CNC Optimization
After completing the heat treatment phase, precise edge profiling becomes the next critical machining operation. You’ll need to optimize your CNC programming parameters to achieve the ideal cymbal edge characteristics while maintaining consistent quality across production runs.
To maximize your edge profiling results, follow these essential steps:
- Configure your CNC tool paths with variable feed rates that adjust automatically based on material thickness and hardness measurements taken during the previous heat treatment phase
- Implement real-time tool wear compensation algorithms to maintain precise edge geometry throughout extended production cycles
- Program micro-adjustments in cutting depth and angle to account for material spring-back, especially in thinner cymbal sections
- Set up automated quality control checkpoints that verify edge profile dimensions against digital templates every 50 cycles
You’ll find that these optimizations notably reduce variation in edge profiles while increasing overall production efficiency and cymbal consistency.
Conclusion
You’ll find these CNC innovations working in harmony like a precision orchestra, where each technique plays its distinct part in the cymbal’s final sound. Just as a conductor guarantees perfect timing among musicians, the automated systems maintain consistency across production runs, with digital hammering alone achieving a remarkable 99.7% strike precision rate. Together, these advancements deliver unprecedented manufacturing control and acoustic excellence.